Wow, talk about a roller coaster day. When we left off last time, I’d dimpled E-606PP where I was supposed to countersink, and I stopped the work day right there while I decided how to handle that little mistake. After some hearty discussion with the hive mind at VAF, it seemed that the best course of action was to flatten the dimples I’d created, countersink the piece like it was supposed to be, and move on. Just to make sure, I performed a test on a piece of scrap of the same thickness as E-606PP; I drilled a #40 hole, dimples that holes, flattened that dimple, and then checked the flatness of the material and the hole size. Hole size looked good, and while the material wasn’t perfectly flat, it was certainly acceptable.
Hooray, I don’t have to throw yet another piece in my scrap pile! Or so I thought…I immediately got to work with the squeezer and flat sets, going down the line and flattening those pesky dimples. Nothing to it…hmm, wait…now the spar piece looked like it had developed a bit of a bow, and was no longer straight. I attempted to cleco it in place on the elevator skin…yup, it is definitely no longer straight. Hmm…well, luckily, I do have tool specifically designed for straightening pieces like this; in fact, it gets used on pretty much every rib with a curve on the plane. So I broke out the fluting pliers and went to work on the spar flange. Five minutes later, and it was straight again.
Oh, wait a second…the whole reason I had to flatten those dimples was because the hinge attaching the trim tab needed to sit flush against the inside of the spar flange, which I had just proceeded to put little flutes in. Well, maybe it’ll be OK once I get everything together…I went ahead and broke out the countersink. After setting the depth properly (a trial-and-error affair I don’t particularly enjoy), I went to work on the spar. The very first hole I countersunk…something didn’t quite feel right as I was doing it. I pulled the countersink bit out, and somehow I’d managed to wallow the hole out to an oblong shape. Clearly this spar just wasn’t meant to go on my aircraft. Into the junk bin you go!
In retrospect, it was probably trash as soon as I decided to flute it. I don’t think that assembly would have gone together right with those flutes in place. It just so happened that I buggered up the countersinking, which in turn made me make the decision to replace.
This, in turn, changed my plans for the day significantly. Originally, I’d wanted to fix E-606PP, go clean all my skeleton parts, and then shoot primer on them once they’d dried. Then I’d have everything ready when it came time to rivet the elevator. Well, there’s no point hurrying to prime everything when I’m going to have to wait for a replacement part. Instead, I decided to attack the “ears” for the trim tab and the elevator trim tab cutout. These things have a pretty solid reputation among RV builders as Things That Are Frequently Buggered Up. I figured I’d go ahead and go after them, and if I messed something up, I could at least order all the replacement parts at once and save on shipping.
A little more on these bends: The trim tab, as well as the edge of the trim tab cutout in the left elevator, don’t have ribs like the ends of most other surfaces. Instead, there’s extra material on each side of the skin; these little tabs are bent down and riveted together to close off the ends of these pieces. Many builders, frustrated with the difficulty of getting these bends right, have taken to simply cutting the tabs off and fabricating custom “riblets” instead. (example) Over the past couple of days, knowing that this task was ahead of me, I did quite a bit of reading on the subject, seeing how other builders had done the bends. Opinions on the task ranged from “not really that bad” to “nigh impossible.” (I’m paraphrasing here; I don’t think I’ve actually run across a build log yet that used the word “nigh” in a sentence) Anyways, I decided to go ahead and try the bends.
If one is following the instructions, one will end up bending the tabs on the elevator first. Which I did, which was, in retrospect, a mistake. There’s a lot more stuff in the way of the job in the elevator than the trim tab, plus there’s just a lot more material around that you have to work around while bending. I know that now, but I didn’t know that when I started this task. So first up, I endeavored to fabricate a bending block. The instructions say to use wood or particle board; I happened to have some scrap MDF left over from my workbench build, so I decided that would work well. A little work with the band saw and belt sander, and I had this little guy:
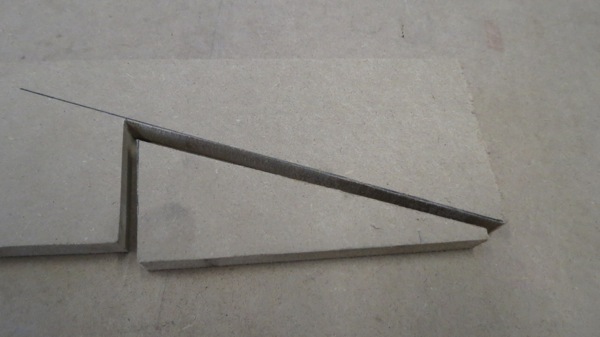
He seemed to be up for the task. OK, next step, mark the bend line on the elevator. Here again, access is kind of difficult; after a few attempts to wrangle a square and Sharpie in there to make the line, I adopted a plan B. I went ahead and stuffed the inside portion of the bending block in place, then used the square to move it around until it was square to the cutout area and in the proper position. Then I used the Sharpie to mark where the block would sit. Now I needed to secure the block in place. The instructions say to use double-sided tape, but I didn’t have any around. No problem, surely the old trick of making a tiny roll of single-sided tape would work, right? (Spoiler alert: the answer is NO) With my blue masking tape in place, I got the block in position, added the outside piece on top, and clamped the thing down. Then I got another block of wood and started tapping on the tab. Oh cool, it’s starting to bend…oh crap, the inside bending block is moving out of place. ABORT!!! Great, now I have a slight bend that’s too far in and not straight at all. I tried resetting the whole jug and bending again, but the block moved again and I just made the nasty bend worse. OK, it’s time to stop and rethink this thing.
This was the first time in a while that I really let a mistake get to me. I’ve been pretty good about taking things in stride, fixing them or replacing stuff as needed, and moving on if possible. This time, though, I was facing replacement of the whole elevator skin, probably $100 in parts at a time when I’m already worried about getting the funds set aside to pay the balance of my wing kit. Rationally, I knew I could probably save the elevator skin, but it was one of those time when emotion completely overrules rationality.
I went inside to do some more reading on the subject. After about 30 minutes of actually reading, instead of just skimming for the stuff I wanted to hear, I learned that there were a few key points to getting these bends right: Using hard material for the bending block, using good double-sided tape to ensure the block didn’t move, and making sure the assembly was clamped very, very tight. I’d been using a couple of these clamps; they’re great for general use, but there’s a limit to how much clamping pressure they can exert.
So off I went to visit Lowe’s Aviation Supply; half an hour later, I was back home with a chunk of red oak, two 6″ C-clamps, and a $10 roll of carpet tape, which I was about to use maybe 2% of before putting the rest of the roll on a shelf for eternity. Oh well, such is homebuilding.
I set about making a new bending block set. The first time, I’d tried to measure the angle of the elevator trailing edge and recreate that; this time, going off another idea I’d read, I used the elevator root rib to get the angle right and draw my cut line. The result was much better-looking than my first attempt. I also decided to bend the trim tab and then move on to the elevator if I could get the technique right. A bunch of careful minutes later, I had the block in place inside the root end of the trim tab:
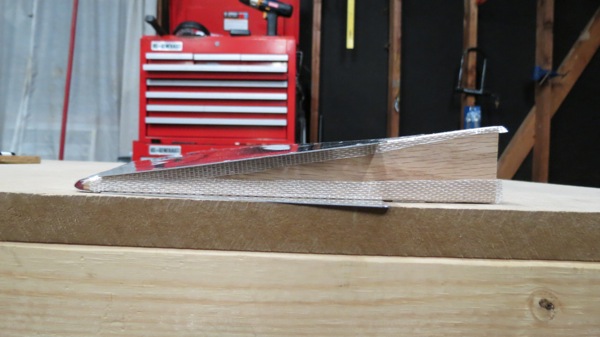
…and clamped down with the other half of the block setup:
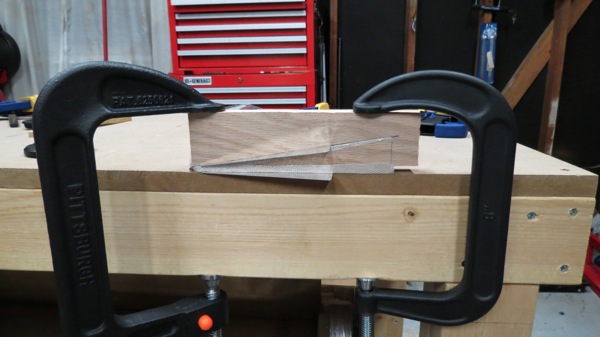
Once again, I went to work with a hammer and a block of wood. This time, things went great, actually beyond my wildest expectations. After getting the bend mostly done, I finished it with the rivet gun and flush set, then repeated the process on the top side. It came out looking absolutely beautiful:
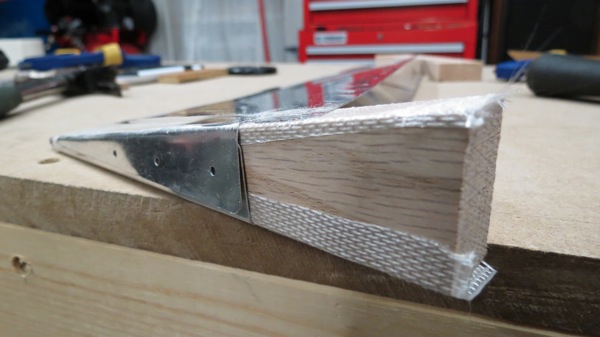
Repeating the process on the other end of the tab was a piece of cake. It went so well, in fact, that I decided to capitalize on my rejuvenated work day and try to save the elevator. The one good thing was that the bend I fouled up was on the bottom of the elevator; if I could flatten it enough to be safe, but not necessarily perfect-looking, at least the only people that would notice would be small children…
So I got the elevator skin back out, cleaned the tape off the bending block, stuck it in the trailing edge, and used it as a backer while I worked over the bad bend with the rivet gun and the flush set. I wasn’t able to straighten it out completely, but it was definitely OK to try bending again. So I did the whole deal again. It was a little tougher this time; the inboard trim tab cutout part of the skin gets in the way of bending the forward part of the tab. I ended up doing the rivet gun portion in two stages; I’d hit the trailing edge area as much as possible, then move one C-clamp so I could get at the rest. The result wasn’t as perfect as the trim tab, but still acceptable to me:
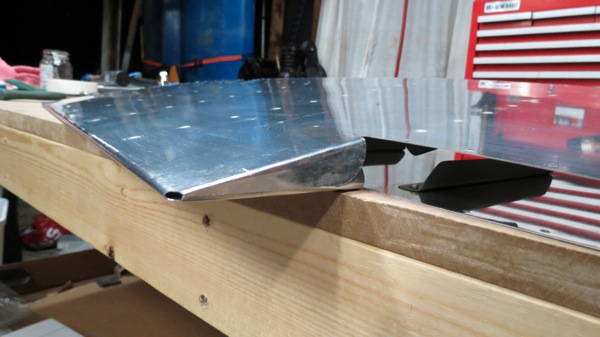
The only concern I have came when I got out that trim tab skin and held it in place on the elevator. Right now, the outboard edge is barely making contact with elevator tabs that I bent. At first I thought maybe I should have bent the elevator tabs further in, but I couldn’t do much more without them interfering with each other. However, upon closer inspection, the tabs on both the trim tab and elevator aren’t bent quite to ninety degrees; I think once both spots are riveted in place, it will pull the tabs in enough to eliminate the contact. If not, I may have to order another trim tab and bend it a little differently to shorten the whole unit a touch. Hopefully that won’t be necessary…I’ll probably seek the feedback of the VAF folks on this one too.
So all in all, quite a day. I went from small failure to larger failure to great success, and ended up at “I think this is going to be OK.” Roller coaster indeed.
EDIT: OK, after further consideration and inspection, I’ve decided to cut out the bent areas in the elevator and fabricate a riblet to go in there. I got to thinking about the clearance issues, looked at my preview planes for clearance specs between the trim tab and elevator, and got concerned about being able to meet the minimum clearance. I decided to run out to the garage and clamp the ears together to sort of “preview” what the ears would look like once they were riveted. When I did that, I suddenly noticed that the elevator bend isn’t even straight; towards the trailing edge, it curves outward, and that’s where my clearance problems would be. Not good enough for my plane, so it’s coming out.
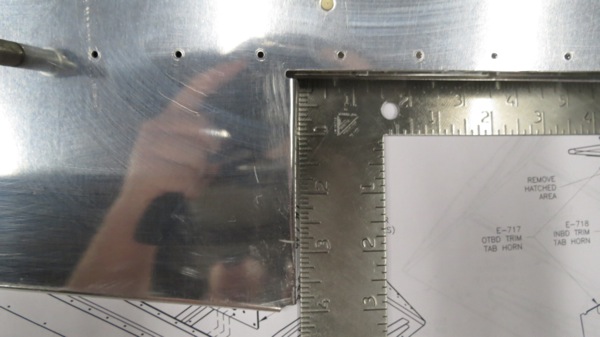