Confession: the hours logged here are pretty much a wild guess. I think I’ve had five or six nights in a row where I was just about to fall asleep and remembered I hadn’t written anything up about the build. Which is to say, I’ve been doing stuff, but not really keeping up with the build log.
When we left off last time, I was about to start worrying about the latch setup for the oil door. As previously mentioned, the approach here will be to use regular old piano hinge, with a bowden cable to release them. The first step was to plan how I’d lay out the hinge halves. At first I got really hung up on wanting the edges of the eyelets on the door to line up with the edges. That was a problem because the door opening is about 1/4” narrower than the eyelets I’d want to line up. I started to think of crazy ways to handle that, before realizing that it was unnecessary.
I started by laying out the hinge on the cowl side. I cut a piece of hinge long enough to cover the opening, plus have an extra eyelet on the forward side, to act as a guide for the cable. I also spent a lot of time trying to think through how to ensure the hinge on the door would clear the cowl, and finally I decided to just line the cowl side of the hinge up with the opening and call that sufficient. That meant I could just go ahead and attach the hinge to the cowl without worrying about fitting everything beforehand.
So I laid out the rivet holes, drilled the hinge and cowl together, and got everything prepped. As usual for metal-fiberglass bonds, I mixed up some loose flox and painted the joint with it before riveting things together. Another consideration here is that due to the recess of the door flange, the part of the hinge that projects forward sits a good bit above the cowl interior. To handle that, after I’d painted on the loose flox, I thickened the mixture up and put a big blob under that forward projection, to fill that gap. The next morning, it had cured up nicely:
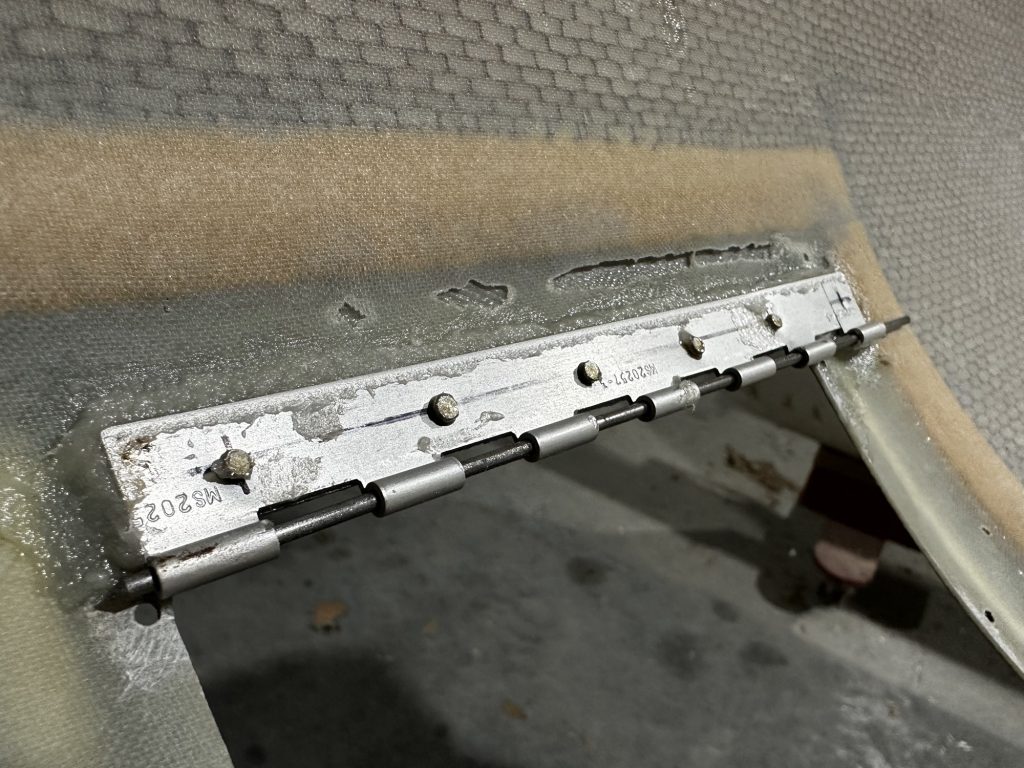
Next up was the hinge half on the door itself. The big consideration here was shining the hinge off of the door to get it to mesh nicely with the other half. My initial measurements indicated that some .063” aluminum would work nicely, so I cut a shim off some scrap and went ahead and riveted it to the hinge I’d cut. Things seemed to line up nicely, and I drilled the rivet holes to attach that stack to the door.
But once I was testing the door movement, the hinges wouldn’t mesh any more. Seems that I needed a little more shim action – so I ended up cutting another shim out of .032” scrap (I think), and I got to drill out the rivets in my hinge-shim stack and add the extra shim. With that in place, things lined up very nicely. After testing the door action a bunch more times, I decided it was time to permanently attach everything else – not just the latch hinge half, but also the actual hinge pieces, to the cowl and door. I wanted to do all these at once so as not to waste epoxy – even one pump of epoxy yields about five times more flox than is needed for just one of these joints.
I did take a different approach to these joints. Previously, for these metal-glass joints, I painted on the flox, clecoed things together, and riveted immediately. This was invariably a messy experience; this time, I decided to try just checking things, letting the flox cure, and then come back to do the riveting later. This worked out pretty well – though for some reason I didn’t take any pictures of any of this work…
After going back and riveting, it was time to put everything together and test the fit and action of the door. Things worked pretty well, but the one thing I noticed that bothered me was that the door didn’t quite sit flush with the cowl once I had the spring installed in the hidden hinge. It seemed that that spring – which is there to make the door pop open when it’s unlatched – was pushing up on the hinge side of the door just enough to keep it from sitting flush.
I was able to close the gap a bit simply by tweaking the hinge itself, but it still didn’t really get the job done. I suspected that the flexibility of the door itself was contributing here, and I spent a fair amount of time trying to think of ways to add some stiffeners to the inside of the door, but none of the ideas I had seemed like they’d be especially pleasant to implement.
Then I read an absurdly simple solution on another build log, where the guy simply used the piece cut out of the cowl, epoxied to the back of the door, to add stiffness. Since that piece, by definition, already has the same curve as the door it ought to work well. And here was a case where my poor shop cleaning habits worked in my favor – I still had the original piece I’d cut out of my cowl sitting on the work bench.
It was still plenty big enough for this job, so I got to work. The big fun here was to do the necessary trimming to get it to fit inside the door. I went a little above and beyond by having it extend around the edges of the hinge; probably unnecessary, but since that was the exact area where the door was popping up, I wanted to add rigidity as far in that direction as possible. So instead of just cutting a nice square-ish piece, I had to carefully fit a cutout around the hinge.
Here’s a look at the trimmed cowl piece after trimming. I’d already added some masking tape in preparation for the impending application of epoxy:
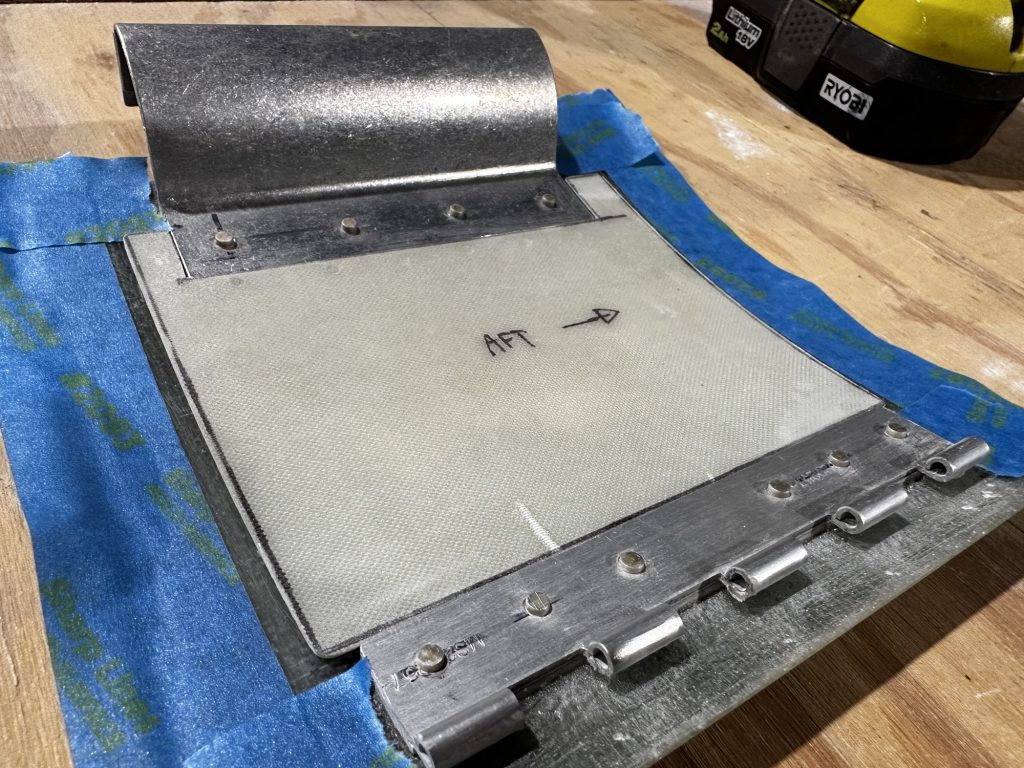
Next, I drilled the two pieces together so I could use clecos to hold them while epoxying, did a whole lot of work to rough up the mating surfaces, and also added packing tape on the cowl flanges. The last thing I wanted to do was accidentally epoxy the door to the cowl, after all.
Then it was time to make another batch of flox, paint the surfaces again, cleco everything together, and clean up all the squeeze-out. After that, I reinstalled the door on the cowl, making sure to use both the hinge pins as well as the cleco holes I drilled on the perimeter, to hold the entire assembly in the exact position I wanted it, and thus ensure that it cured with the desired shape.
Here’s a look at the assembly just before I added the perimeter clecos; the packing tape on the flange is clearly visible:
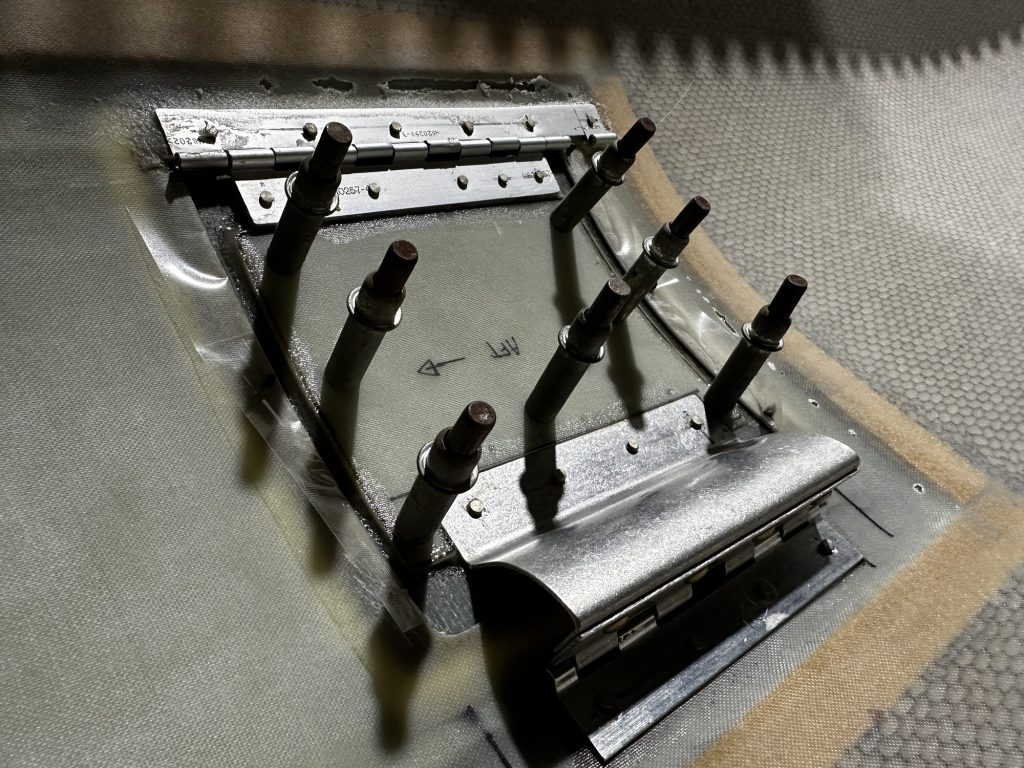
The next morning (this morning, actually) was the age-old fiberglass routine: go find out if I accidentally glued two things together that weren’t supposed to be. It’s always a bit of a relief when the parts that are supposed to separate do just that.
I revisited the setup after work; the big question mark was seeing if this stiffening actually helped the fit problem I was trying to solve, or if I’d just wasted time. I’m happy to report that it now fits up very nicely. I may still sand down the top forward corner (lower right in the photo below) just to really fine-tune things, but it looks pretty good as-is:
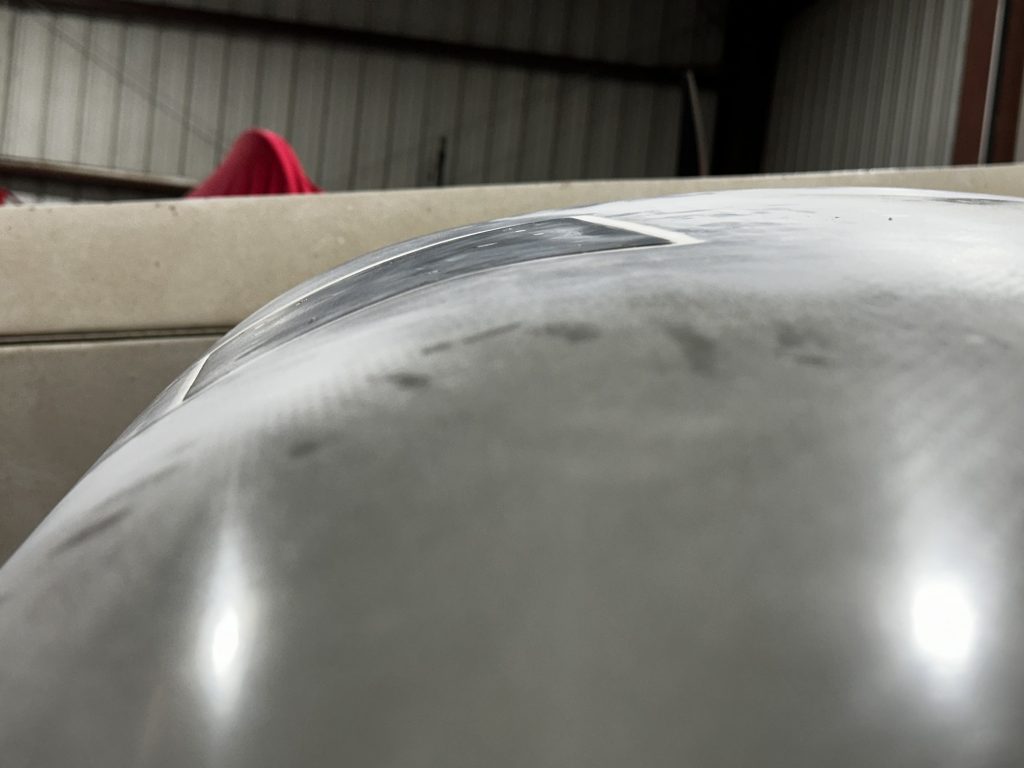
I also spent some time sanding off excess epoxy inside the door; it seemed like a lot more squeezed out while this was curing. I tried to make a nice semi-rounded transition between the door and the reinforcement, mainly so there aren’t annoying sharp edges here, but also just because it looks nicer. And finally, it was time for one more function check of the door. It’s a little rough popping up when the latch pin is pulled, but I think I can fine-tune that just by sanding the edges of the eyelets where they contact. For the most part, though, the thing pops up nicely:

I told someone this weekend that when the oil door was done, I was probably done with fiberglass for a while. Technically, I do still need to take care of glassing in the cooling ramps on the upper cowl, and it’s looking like I am still going to need to add a blister to clear the mixture arm, but I think I’m about ready to switch gears for a while. Plus, it’s supposed to cool off later this week, and low temperatures don’t really agree with fiberglass – if it’s cold, the epoxy won’t kick off and cure properly.
So I’m going to pull the engine baffle kit out of the bin and get back to work on that. I think it’ll be nice to get back to doing some regular old sheetmetal work.